Συσκευές Mέτρησης για Θερμοηλεκτρικά – LSR Thermoelectrics
Το σύστημα LSR Thermoelectrics της Linseis μετρά τις βασικές ιδιότητες των θερμοηλεκτρικών υλικών, όπως τον συντελεστή Seebeck, την ηλεκτρική αντίσταση και τη θερμική αγωγιμότητα. Παρέχει ακριβείς και αξιόπιστους υπολογισμούς για την απόδοση των υλικών, όπως ο παράγοντας αξιολόγησης (ZT), και είναι κατάλληλο για ερευνητικές και βιομηχανικές εφαρμογές σε ευρύ θερμοκρασιακό εύρος.
- Ανάκτηση Θερμότητας Αποβλήτων (Waste Heat Recovery)
- Θερμοηλεκτρικές Γεννήτριες (TEG)
- Θερμοηλεκτρικά Στοιχεία Peltier
- Αισθητήρες
- Θερμοηλεκτρικά Επιθέματα
- Θερμοηλεκτρικές Μονάδες
LSR Thermoelectrics
The LSR can simultaneously measure both the Seebeck coefficient and the electrical resistance (thermal conductivity and ZT using the Harman method).
- Prismatic and cylindrical samples with a length between 6 and 23 mm can be analyzed (prismatic samples required for the Harman method)
- Wires and foils can be analyzed with a special measuring adapter
- Four different interchangeable ovens cover the temperature range from -100°C to 1500°C
- The design of the sample holder guarantees maximum reproducibility of the measurements
- State-of-the-art software enables automatic measurement sequences
- Harman option
Four different interchangeable ovens cover the temperature range from -100° to 1500°C.
In addition, the infrared ovens enable very high heating and cooling rates and the advantage of the most precise temperature control according to the set temperature profile.
Measuring Principle
A cylindrical or prism-shaped sample is placed vertically between two electrodes.
The lower electrode block contains a heater, while the entire measuring arrangement is located in a furnace.
The furnace surrounding the measuring arrangement heats the sample to a certain temperature.
At this temperature, the secondary heater in the lower electrode block generates a specific temperature gradient.
Two contacting thermocouples then measure the temperature gradient T1 and T2.
A unique thermocouple contact mechanism enables measurements of the electromotive force dE on one wire of each of the two thermocouples with maximum temperature accuracy.
The DC quadripole method is used to measure the electrical resistance.
A constant current (I) is applied to both ends of the sample and the change in voltage (dV) between one wire on each of the two thermocouple pairs is measured.
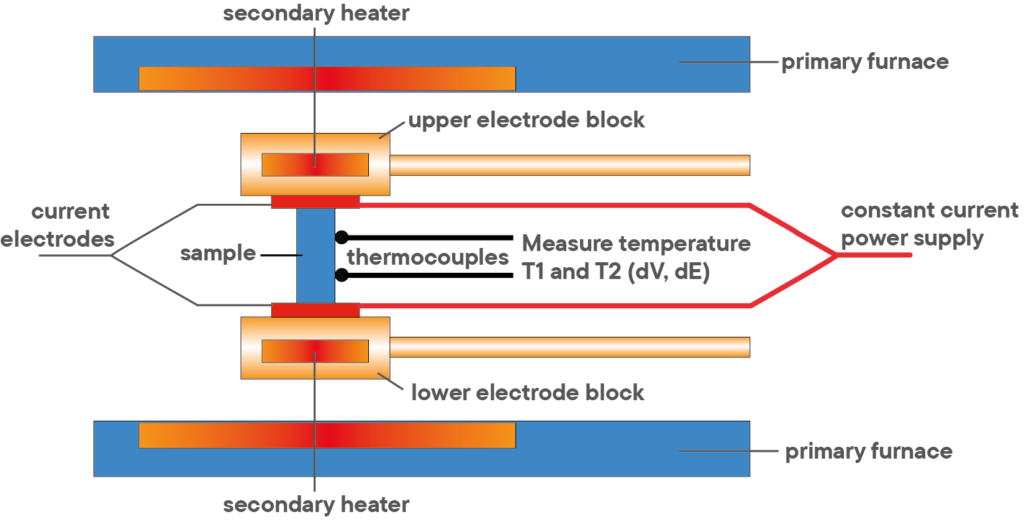
Linseis LSR series
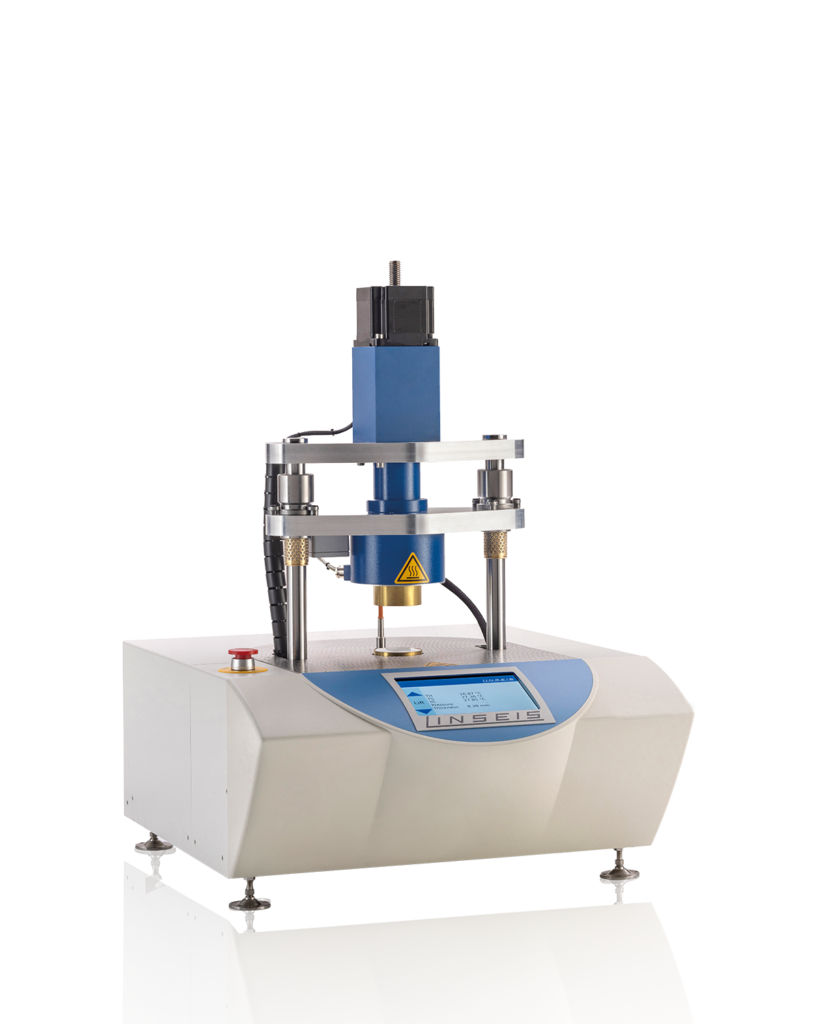
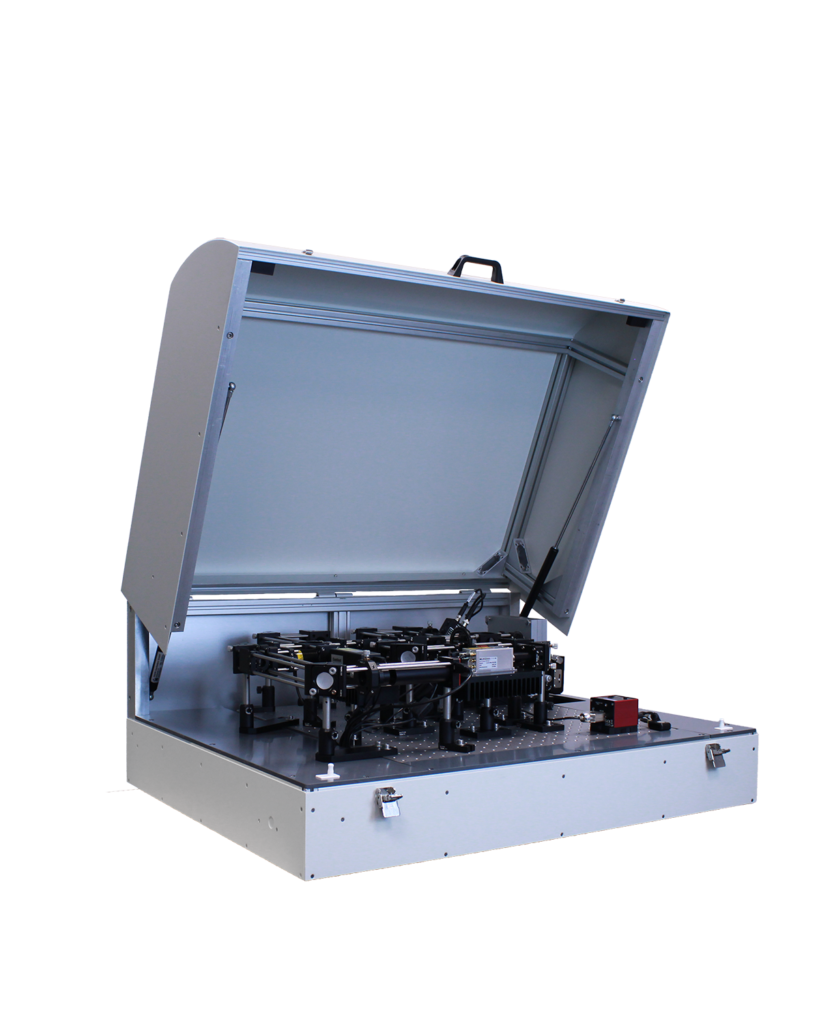
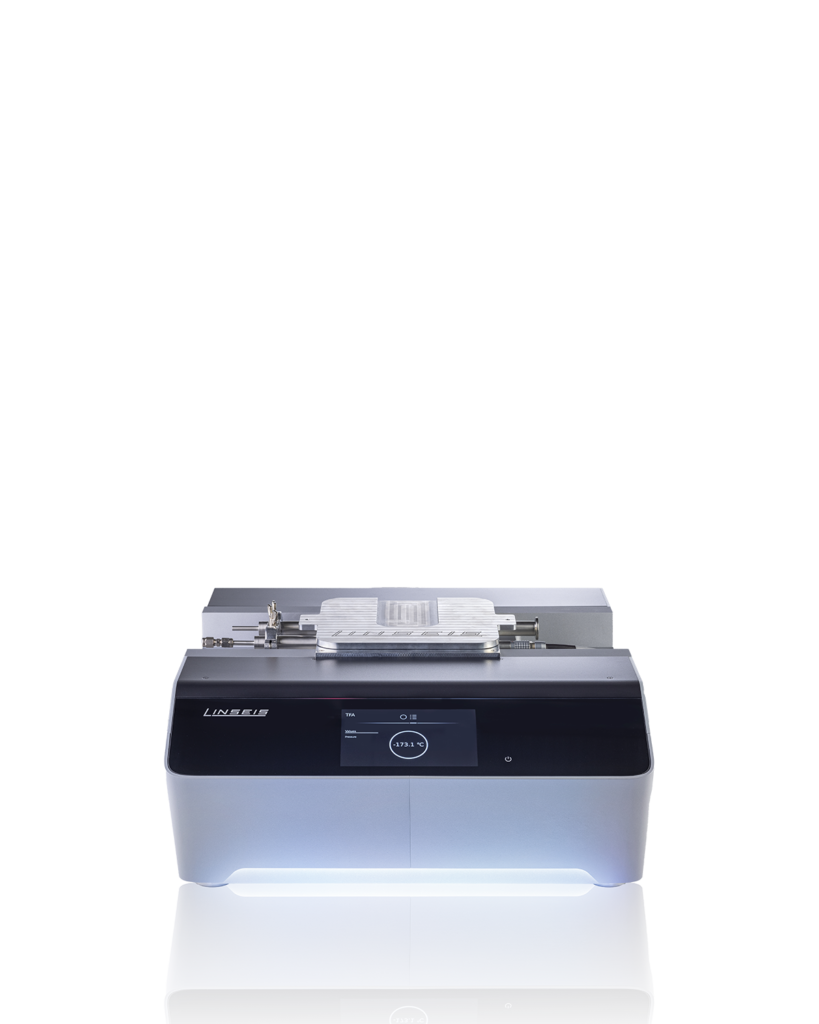
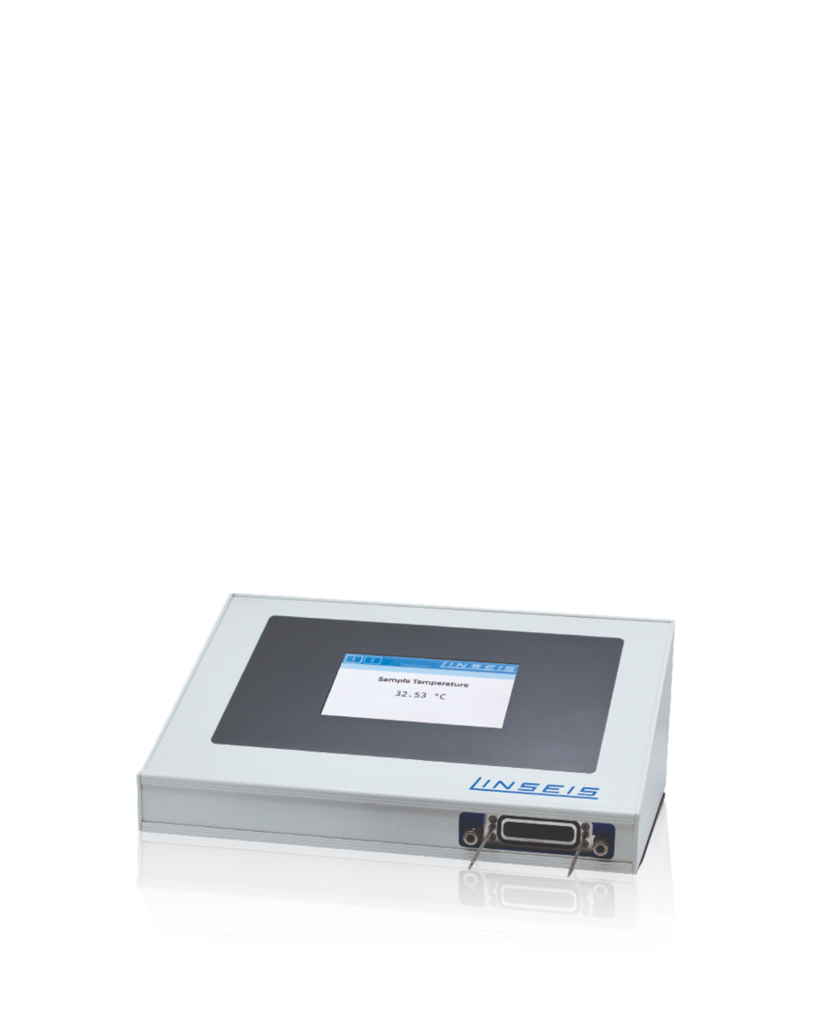
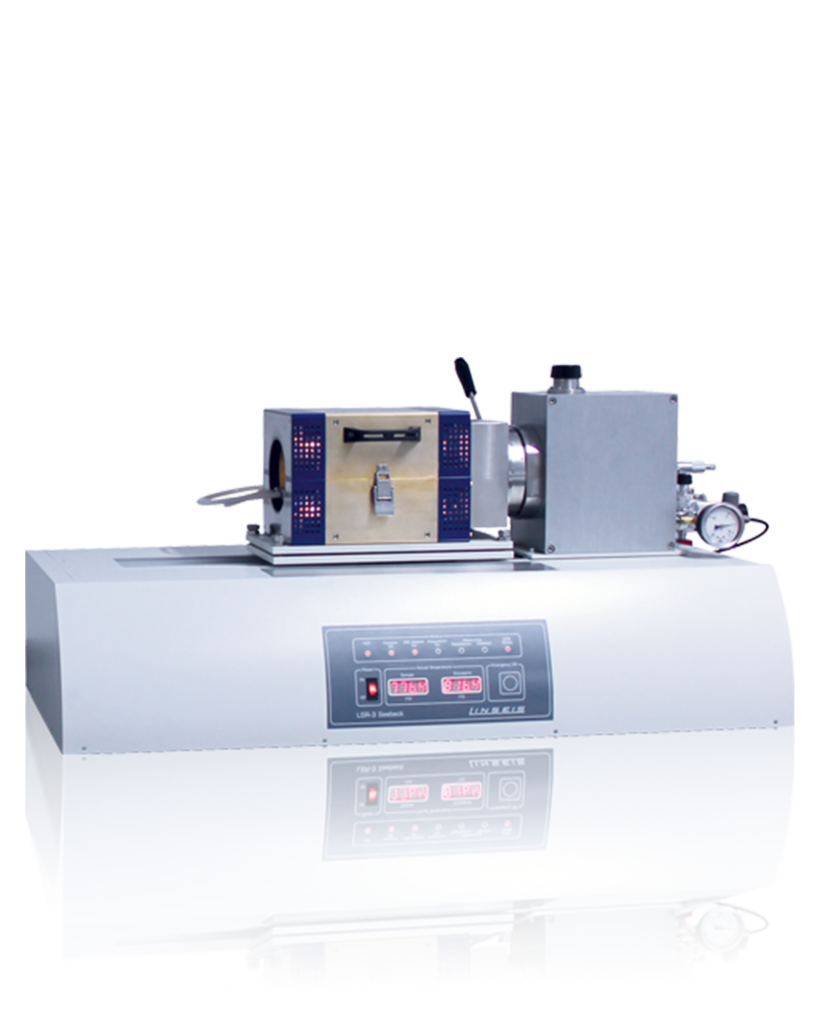
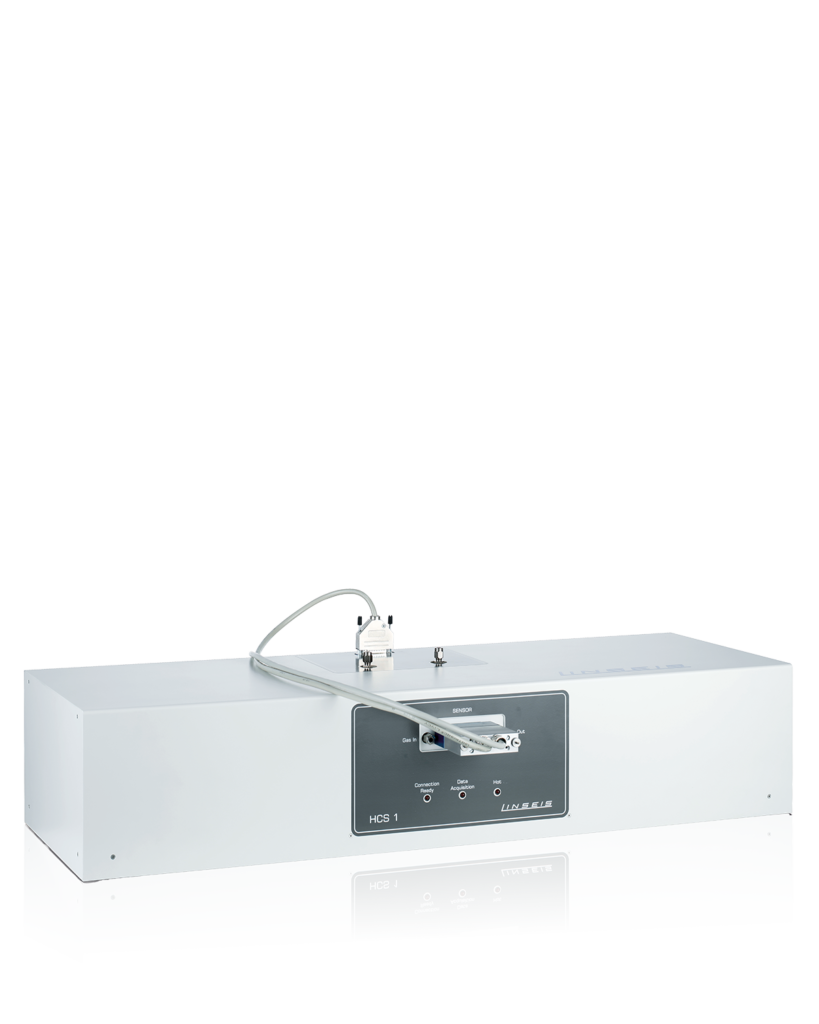
Downloads
ΙΔΑΝΙΚΟ ΓΙΑ
The LSR (Laser Flash System) series by Linseis is ideal for measuring thermoelectric properties of materials, including:
- Seebeck Coefficient: Determines the voltage generated due to a temperature gradient in a material.
- Electrical Conductivity: Measures how well a material can conduct electricity.
- Thermal Conductivity: Assesses the material’s ability to transfer heat.
- Figure of Merit (ZT): Evaluates the efficiency of thermoelectric materials by combining Seebeck coefficient, electrical conductivity, and thermal conductivity.
Applications:
- Thermoelectric Material Development: For power generation or cooling applications.
- Material Research: Understanding the thermal and electrical behavior of metals, semiconductors, and insulators.
- Energy Efficiency Studies: In renewable energy systems, waste heat recovery, and advanced material testing.
The LSR series is particularly suited for high-precision and high-temperature measurements, making it essential for R&D in energy-related materials.
ΧΑΡΑΚΤΗΡΙΣΤΙΚΑ
MODEL |
TEG-TESTER |
---|---|
Sample size: | Round: ø 20 mm, 25 mm, 40 mm, 60 mm Rectangular: 20 mm x 20 mm, 25 mm x 25 mm, 40 mm x 40 mm Other sizes on request |
Sample thickness: | up to 25 mm |
Accuracy of thickness: | +/- 0.10 % at 50% tensile force +/- 0.25 % at 100% tensile force |
Temperature range: | RT up to 300°C (on the hot side) / -20 °C up to 300 °C |
Temperature accuracy: | 0.1°C |
Voltage range: | 0 – 12 V (DC) |
Accuracy of voltage: | 0.3 % |
Voltage resolution: | 1.6 µV |
Amperage: | 0-3 A (DC) |
Current accuracy: | 0.3 % |
Current resolution: | 1 µA |
Heat dissipation: | up to 36 W |
Rating: | Heat Flow Average Seebeck coefficient Average thermal conductivity Average module resistance Power output Conversion efficiency of the module |
Reference block material: | Aluminium, brass, copper (others on request) |
Temperature sensors: | Thermocouple type E |
Clamping force: | 2 kN to 5 kN (electric drive) |
Heating power: | 1.0 kW |
Intracooler | |
Cooling capacity: | 1.0 kW (10 °C) / 0.5 kW (-20 °C) |
Pump capacity: | 27 l/min / 0.7 bar |
Tank capacity: | 3.8 l up to 7.5 l |
Refrigerant used: | R449 Liquid |
MODEL |
TF-LFA |
---|---|
Sample dimensions: | Any shape between 2mm x 2mm and 25mm x 25mm lateral size |
Thin film samples: | 10nm up to 20μm* (depends on sample) |
Temperature range: | RT, RT up to 200/500°C Sample holder for 4“ Wafer (only RT) |
Measured properties: | Thermal conductivity Thermal diffusivity Thermal interface resistance Volumetric specific heat capacitiy Thermal effusivity |
Options: | Anisotrophy: Measurement of cross-plane and in-plane thermal properties Sample mapping: Camera: |
Atmosphere: | inert, oxidizing or reducing vaccuum up to 10E-4mbar |
Diffusivity measuring range: | 0.01mm2/s up to 1200mm2/s (depends on sample) |
Pump laser: | CW Laser (405 nm, 300 mW, modulations frequency up to 200 MHz) |
Probe laser: | CW Laser (532 nm, 25 mW) |
Photodetector: | Si Avalanche Photodetector, active diameter: 0.2 mm, bandwidth: DC – 400MHz |
Power supply: | AC 100V ~ 240V, 50/60 Hz, 1 kVA |
Software: | Included. Software package using multi-layer analysis for calculation of thermophysical properties |
*Actual thickness range depends on sample |
MODEL |
TFA – THIN FILM ANALYZER |
---|---|
Temperature range: | RT to 280°C -160°C to 280°C |
Sample thickness: | From 5 nm to 25 µm (depending on sample) |
Measuring principle: | Chip-based (pre-structured measuring chips, 24 pieces per box) |
Separation techniques: | Among others: PVD (sputtering, vaporisation), ALD, spin coating, ink-jet printing and many more |
Measured parameters: | Thermal conductivity (3 Omega) |
Heat capacity | |
Optional: | Electrical conductivity / specific resistance Hall constant / mobility / charge carrier density (electromagnet up to 1 T or permanent magnet with 0.5 T) |
Vacuum: | ~10E-4mbar |
Electronics: | Integrated |
Interface: | USB |
Measuring range | |
Thermal conductivity: | 0.05 to 200 W/m∙K 3 Omega method, hot-strip method (in-plane measurement) |
Electrical conductivity: | 0.05 to 1 ∙ 106 S/cm Van der Pauw four-probe measurement |
Seebeck coefficient: | 5 to 2500 μV/K |
Repeatability & Accuracy | |
Thermal conductivity: | ± 3% (for most materials) ± 10% (for most materials) |
Resistivity: | ± 3% (for most materials) ± 6% (for most materials) |
Seebeck coefficient: | ± 5% (for most materials) ± 7% (for most materials) |
MODEL |
LSR-1 |
---|---|
Temperature range: | Basic unit: RT to 200°C Cryo option: -160°C to +200°C |
Principles of measurement: | Seebeck coefficient measuring range: 0 to 2.5 mV/K – temperature gradient up to 10K Seebeck voltage measurement: range +-8 mV |
Atmospheres: | Inert, reducing, oxidising, vacuum Helium gas with low pressure, recommended |
Sample holder: | Integrated PCB board with primary and secondary heater |
Sample size (Seebeck): | L: 8 mm to 25 mm; W: 2 mm to 25 mm; D: Thin film up to 2 mm |
Sample size (resistance): | L: 18 mm to 25 mm; W: 18 mm to 25 mm; D: thin film up to 2 mm |
Vacuum pump: | optional |
Heating rate: | 0.01 – 100 K/min |
Temperature accuracy: | ±1,5 °C oder 0,0040 ∙ | t | |
Electrical resistance: | 10 nOhm |
Thermal voltage: | 0.5 nV/K (nV = 10-9 V) |
MODEL |
LSR-3 |
---|---|
Temperature range: | Infrared oven: RT up to 800°C/1100°C Resistance oven: RT up to 1500°C Low temperature oven: -100°C to 500°C |
Measurement method: | Seebeck coefficient: Static DC method / Slope method Electrical resistance: four-point measurement |
Atmosphere: | Inert, reducing, oxidizing, vacuum Helium gas with low pressure recommended |
Sample holder: | Vertical clamping between two electrodes Optional adapter for films and thin layers |
Sample size (cylinder or rectangle): | 2 to 5 mm base area and max. 23 mm long up to a diameter of 6 mm and a length of max. 23 mm long |
Sample size round (disc shape): | 10, 12.7, 25.4 mm |
Measuring distance of the thermocouples: | 4, 6, 8 mm |
Water cooling: | required |
Measuring range Seebeck coefficient: | 1µV/K to 5000 µV/K (static direct current method) Accuracy ±7% / repeatability ±3.5% |
Measuring range Electrical conductivity: | 0.01 to 2×10 5 S/cm Accuracy ±10% / repeatability ±5% |
Current source: | Low drift current source from 0 to 160 mA (optional 220 mA) |
Electrode material: | Nickel (-100 to 500°C) / Platinum (-100 to +1500°C) |
Thermocouples: | Type K/S/C |
* 5% for LSR including camera option |
MODEL |
HCS 1 |
---|---|
Temperature range: | From LN2 up to 600°C in various versions -160°C (controlled cooling) -196°C (cooling) |
Magnet: | Two permanent magnets with +/- 0.7T Diameter of the rod 120 mm for maximum uniformity (+/- 1% over 50mm) |
Power supply: | DC 1nA up to 125mA (8 decades / compliance +/- 12V) |
Voltage measurement: | DC low noise / low deviation 1μV up to 2500mV, 4 decades gain, digital resolution: 300pV |
Sensors/ sample geometry: | – from 5 x 5 mm2 to 12.5 x 12.5 mm2, maximum sample height 3 mm – from 17.5 x 17.5 mm2 up to 25 x 25 mm2, maximum sample height 5 mm – from 42.5 x 42.5 mm2 up to 50 x 50 mm2, maximum sample height 5 mm – High temperature plate, 10 x 10mm2, max. sample height 2mm |
Resistance range: | 10-4 up to 107(Ωcm) |
Carrier concentration: | 107 up to 1021cm-3 |
Mobility range: | 0.1 to 107(cm2/volt sec) |
Atmospheres: | Vacuum, inert, oxidizing, reducing |
Temperature accuracy: | 0.05°C |
MODEL |
HCS 10 |
---|---|
Temperature range: | From LN2 up to 600°C in various versions -160°C (controlled cooling) -196°C (quench cooling) |
Magnet: | Electromagnet up to +/- 1 T variable DC field, pole diameter 76 mm, power supply 75A / 40V. Current reversing switch for bipolar measurement. Alternative AC option for an alternating magnetic field with ~1 T usable field, at a frequency of up to 0.1 Hz |
Power supply: | DC 1nA up to 125mA (8 decades / compliance +/- 12V) AC 16 μA up to 20 mA and input impedance: >100 GigaOhm from 1 mHz to 100 kHz |
Voltage measurement: | DC low noise / low deviation 1μV up to 2500mV, 4 decades gain, digital resolution: 300pV AC 20 nV up to 1V, variable integration times and gain |
Sensors/ sample geometry: | – from 5 x 5 mm2 to 12.5 x 12.5 mm2, maximum sample height 3 mm – from 17.5 x 17.5 mm2 to 25 x 25 mm2, maximum sample height 5 mm – from 42.5 x 42.5 mm2 up to 50 x 50 mm2, maximum sample height 5 mm – High temperature plate, 10 x 10 mm2, maximum sample height 2 mm |
Resistance range: | 10-4 up to 107(Ωcm) |
Carrier concentration: | 107 up to 1021cm-3 |
Mobility range: | 10-3 ~ 107cm2V-1s-1 |
Atmospheres: | Vacuum, inert, oxidizing, reducing |
Temperature accuracy: | 0.05°C |
MODEL |
HCS 100 |
---|---|
Temperature range: | RT up to 500°C |
Magnet: | Magnet up to 0.5 T (AC or DC field) Multisegment Halbach configuration, inner diameter: 40mm, height: 98mm |
Power supply: | DC 1nA up to 125mA (8 decades / compliance +/- 12V) AC 16 μA up to 20 mA and input impedance: >100 GigaOhm from 1 mHz to 100 kHz |
Voltage measurement: | DC low noise / low deviation 1μV up to 2500mV, 4 decades gain, digital resolution: 300pV AC 20 nV up to 1V, variable integration times and gain |
Sensors/ sample geometry: | Up to 10 x 10 mm2, maximum sample height 2.5 mm |
Resistance range: | 10-5 up to 107(Ωcm) |
Carrier concentration: | 107 up to 1022cm-3 |
Mobility range: | 1 ~ 107cm2V-1s-1 |
Atmospheres: | Vacuum, inert, oxidizing, reducing |
Temperature accuracy: | 0.05°C |