Optomechanical devices by Instytut Fotonowy ensure precise light control with low EM emission, ideal for sensitive lab setups.
Description
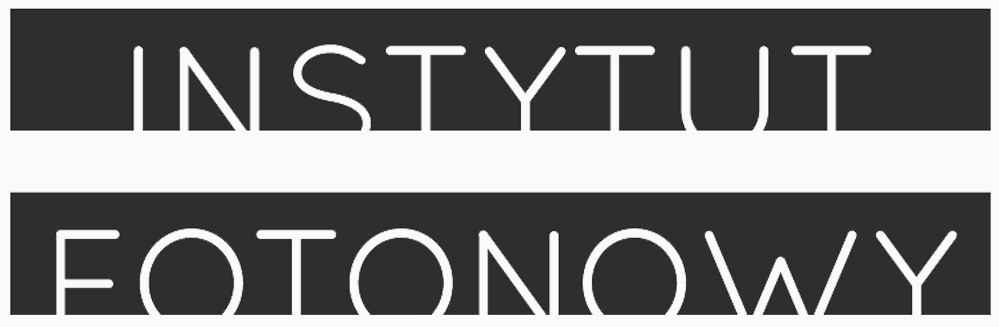
Optomechanics
Instytut Fotonowy’s optomechanical systems offer precise, low-EM emission solutions for optical experiments, including devices such as a motorized multi-axis vacuum table, filter changer, chopper/shutter, motorized iris diaphragm, vertical and single-axis translation stages, multi-axis and long translation stages, and a bioluminescence setup, all designed for smooth integration and accurate control in advanced laboratory environments.
Motorized multi-axis vacuum table
The Motorized Multi-Axis Vacuum Table is a compact solution which may be used in a wide range of applications where the precision of positioning is significant. The table is equipped with a vacuum system for holding a sample in place.
The table may be equipped with a built-in light sensor of any type, installed at the table surface. An additional metallic coating may be deposited on the surface to provide appropriate electrical contact with the sample.
Specifications:
⬛ Motorized and Manual regulation of position in two axes: X and Y
⬛ Stroke in X and Y axis: 20 cm
⬛ Movement precision: 0.01 mm
⬛ Manual regulation of table height in Z axis
⬛ Stroke for Z axis: 12 mm
⬛ Maximum sample size: 20 x 20 cm
⬛ Vacuum system for sample holder
⬛ Optional table surface coating: golden or chromium
⬛ Optional contact electrodes, manually placed at any point of the sample
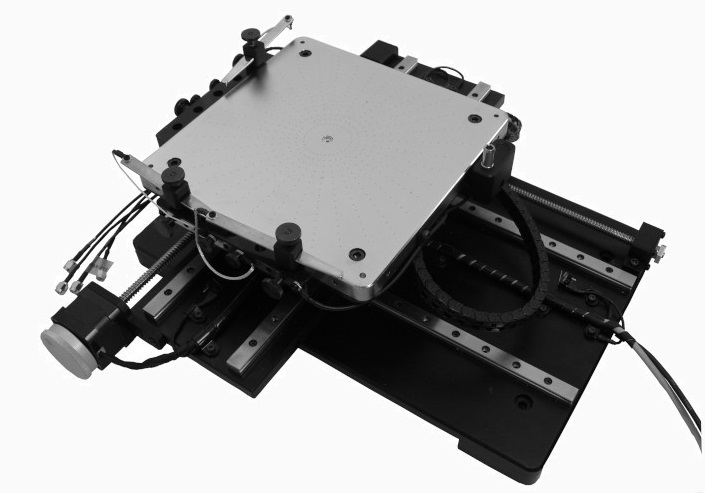
Filter Changer

The Filter Changer is designed to hold six Ø1″ filters up to 8 mm (0.30″) thick. The carousel allows quick and accurate switching between filters. The ZF series of filter wheel stations offers compact and versatile filter organizers, available in single- or multi-wheel configurations. Each carousel can accommodate six filters and rotate independently. This model can be controlled manually via a push button, or remotely through an RS-232 interface.
Specifications:
⬛ 6-station carousel with multi-wheel configuration system available
⬛ Internally SM1-threaded (1.035″) holes for Ø1″ filters up to 8 mm (0.30″) thick
⬛ THORLABs cage system compatibility (4-40 UNC threads)
⬛ Manual or Automated control (via RS-232 or RS-485 interface)
Low EM Emission Chopper/Shutter
The device can operate in chopper mode (5 Hz – 10 kHz) or shutter mode (0 – 10 Hz), offering flexibility for various experimental needs. The chopper mode is ideal for phase-sensitive measurements and can be seamlessly integrated into any lock-in setup that sends or receives a TTL modulation signal. In shutter mode, a two-slot blade is used, which can either remain stationary indefinitely or switch on and off with a minimum transition time of 0.05 sec, allowing for precise control of light exposure.
Specifications:
⬛ Chopper mode: 5 Hz (with two-slot blade) – 10 kHz (with 100-slot blade)
⬛ Shutter mode: 0 Hz – 10 Hz
⬛ Slots: compatible with Thorlabs 2, 10, 15, 30, 60, 100 blades
⬛ Blade diameter: 4 inch (custom diameters available)
⬛ Set frequency resolution: 0.01 Hz (two-slot blade), 1 Hz (others)
⬛ Set phase resolution: 0.1 degree
⬛ Included blades: 2-slot and 10-slot blades
⬛ Synchronization capabilities: internal and external signal sync
⬛ Internal/external synchronization: harmonics 1–15, subharmonics 1/2 – 1/15
⬛ Synchronization input: 0–5 V BNC
⬛ Synchronization output: 0–5 V BNC
⬛ Controller interface: front panel buttons or PC via USB
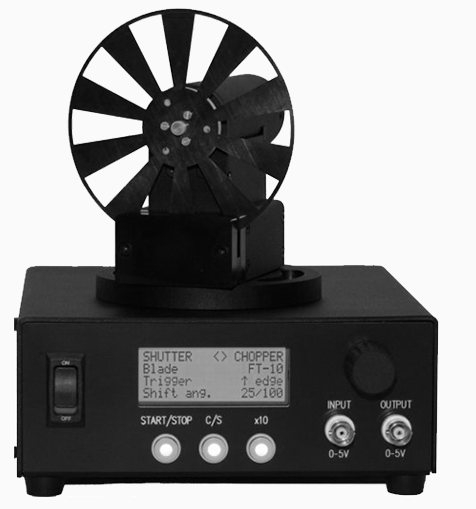
Motorized Iris Diaphragm
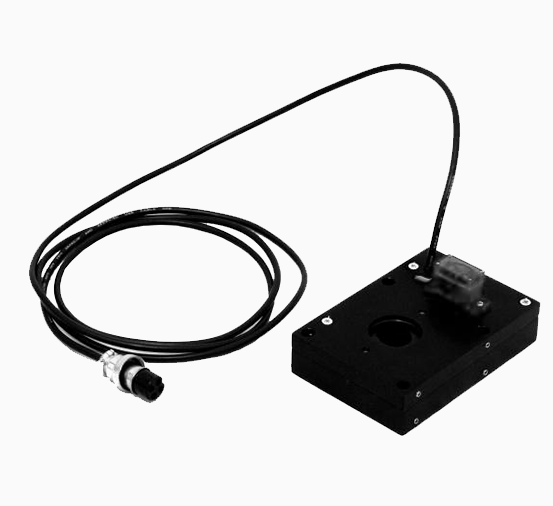
The Motorized Iris Diaphragm is designed for automated mechanical adjustment of the light beam size and intensity using a servo motor. It enables precise control of the aperture, making it ideal for optical experiments requiring variable light exposure. The device is housed in a durable anodized black aluminum enclosure and is RS232-controllable, ensuring easy integration into laboratory setups.
Specifications:
⬛ 100 possible iris positions
⬛ Maximum aperture: 25 mm
⬛ Minimum aperture: 0 mm
⬛ Controlled via RS232
⬛ Power supply: 5 V
⬛ Housing: anodized black aluminum
⬛ Dimensions: 105 × 72 × 35 mm
Vertical Translation Stage
The Vertical Translation Stage is a stable and highly adaptable platform designed for precise vertical positioning in laboratory setups. Its scissor-shaped lifting mechanism and double guide rail 5-axis positioning system ensure smooth, accurate movement and excellent load capacity. Featuring a locking hand wheel and multiple mounting holes on both top and bottom, it provides versatility in integration. This stage is ideal for applications requiring non-quantitative raising/lowering over a large stroke range.
Specifications:
⬛ Stroke: 60 mm (Z axis)
⬛ Upper platform size: 120 × 80 × 10 mm
⬛ Minimal height: 60 mm
⬛ Drive mode: abrasive screw pair
⬛ Resolution: 0.01 mm
⬛ Load capacity: 20 kg
⬛ Weight: 1.15 kg
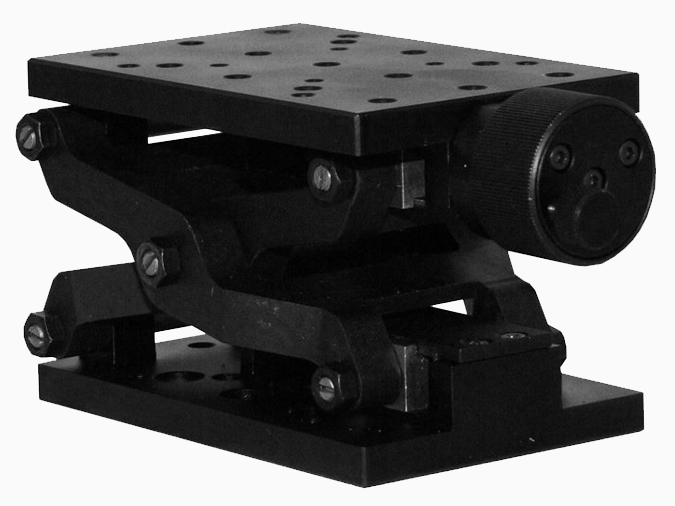
Vertical Translation Stage
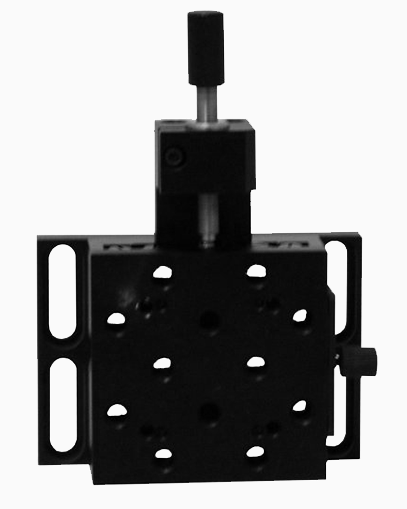
The Single-Axis Translation Stage is a precise and stable solution for linear movement along the X-axis, ideal for laboratory experiments requiring fine adjustment and high accuracy. Its compact design, combined with a center-positioned drive and V-shaped guide rail with cross rollers, ensures smooth motion and reliable performance even under load.
Specifications:
⬛ Adjustable dimension: X-axis
⬛ Drive mode: fine adjustment screw thread pair
⬛ Drive position: center
⬛ Guide rail: V-shaped with cross roller
⬛ Stroke: 25 mm
⬛ Accuracy: 1 µm
⬛ Load capacity: 10 kg
⬛ Weight: 0.6 kg
Vertical Translation Stage
The Multi-Axis Translation Stage offers precise movement along the XY plane, making it ideal for laboratory setups that require fine, stable, and coordinated adjustments in two dimensions. With a compact and robust design, V-shaped guide rails with cross rollers, and center-positioned fine adjustment screws, this stage ensures high accuracy and repeatability in experimental positioning tasks.
Specifications:
⬛ Adjustable dimensions: XY
⬛ Drive mode: fine adjustment screw thread pair
⬛ Drive position: center
⬛ Guide rail: V-shaped with cross roller
⬛ Stroke: 25 mm
⬛ Accuracy: 1 µm
⬛ Load capacity: 10 kg
⬛ Weight: 1.1 kg
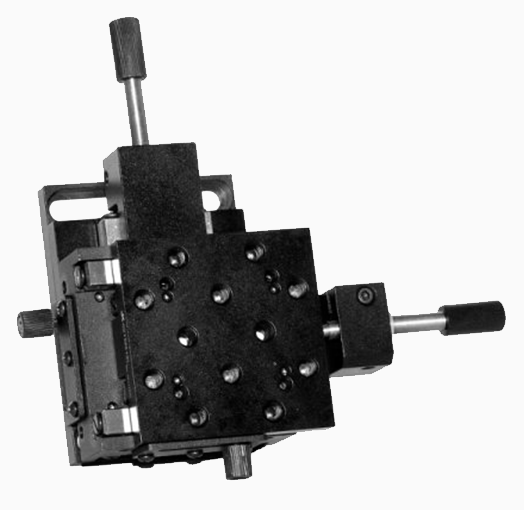
Motorized Long Translation Stage
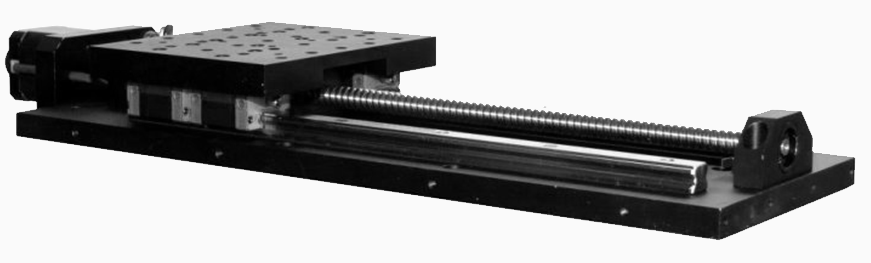
The Motorized Long Translation Stage is a high-precision, motorized positioning platform ideal for applications that require extended linear motion with excellent repeatability and stability. Its robust design, linear bearing guide rail, and automated control make it particularly suited for demanding laboratory experiments involving large samples or instruments.
Specifications:
⬛ Stroke: 250 mm
⬛ Table top size: 120 × 150 mm
⬛ Guide rail: linear bearing
⬛ Screw load: 4 kg
⬛ Resolution: 2.5 µm
⬛ Maximum speed: 40 mm/s
⬛ Repeat positioning accuracy: < 5 µm
⬛ Motor step: 1.8°
⬛ Maximum static torque: 40 Ncm
⬛ Central loading capacity: 30 kg
Bioluminescence Setup
The Bioluminescence Setup is a highly sensitive detection system designed to measure ultra-low light emissions, such as single photons resulting from bioluminescent or chemiluminescent processes in plants and other biological samples. It is particularly effective for capturing the faint light produced by chemical reactions in living cells, including those in fresh fruits and vegetables, before internal processes cease. The setup provides high quantum efficiency, especially at 410 nm, making it ideal for advanced biological and biochemical research.
Specifications:
⬛ Spectral range of detector: 185 nm – 710 nm
⬛ Measurement accuracy: adjustable via discrimination threshold (single photon detection possible)
⬛ Maximum sensitivity: at 410 nm
⬛ Quantum efficiency at 410 nm: 23%
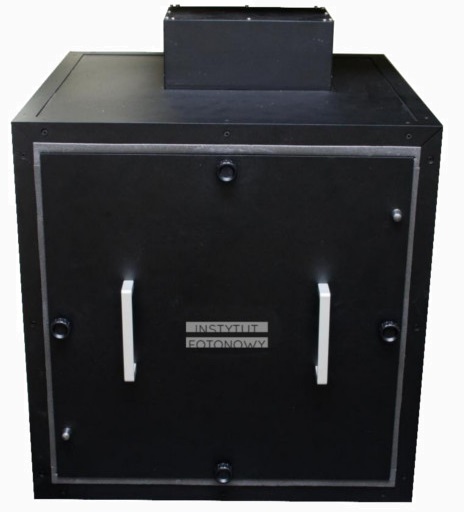